Salmon Technologies
Norwegian salmon farming is the result of decades of hard work, courage and a strong desire to succeed. New ideas and the development of ground-breaking technologies have been crucial in making Norway an aquaculture nation, daily shipping 37 million salmon meals all over the world. What started out as a small hobby project, with pieces of plank and some nets, has now developed into a great industry with job creation all along the coast.
Here, you can immerse yourself in the different parts of the production, from broodstock to harvestable fish. You also meet the different companies that have developed ground-breaking technologies in the aquaculture industry. Lastly, some of the challenges are highlighted, as well as the progression of the work aiming to resolve them.
Broodstock fish
Breeding
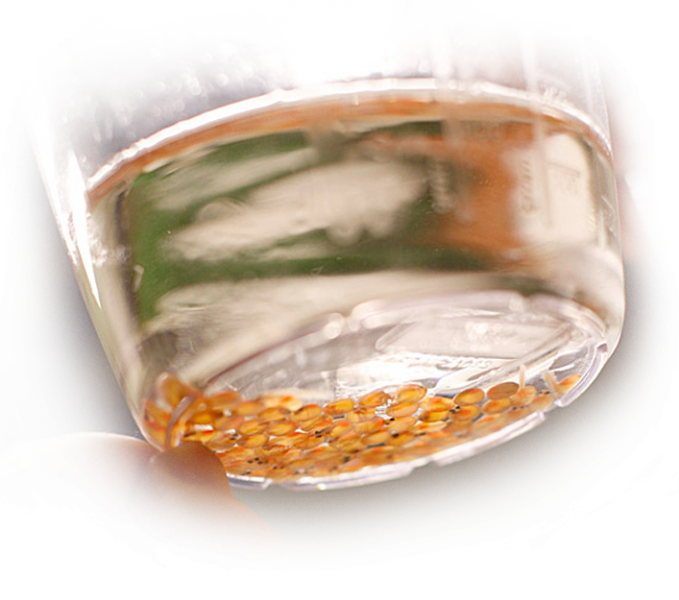
The farmed salmon is well accustomed to life in aquaculture facilities. This is due to years of thorough work in developing the right characteristics for the fish. The best fish are selected to parent the next generation. This process is called breeding, and we have carried it out systematically in Norway since the 1970´s. The results are farmed salmon showing rapid growth and strong immune systems.
The aquaculture industry depends on highly advanced technologies from companies all over Norway. Navigate right to explore these.
Broodstock fish
AquaGen
Infectious pancreas necrosis (IPN) is one of the most infectious diseases in fish farming. AqueGen is one of the companies working on this challenge, and the first to deliver salmon roe immune to the disease.
AquaGen produces salmon roe for aquaculture companies in Norway and abroad. Through research and systematic breeding, they ensure that each new generation of farmed salmon displays better growth and resilience to diseases, than the previous generation.
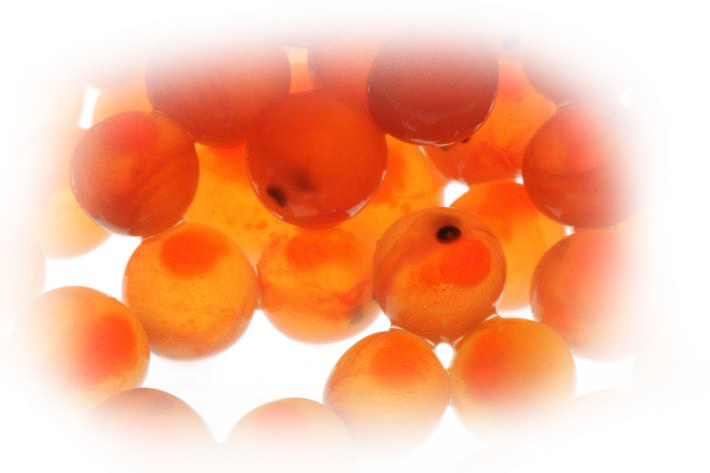
Hatchery
Hatchery
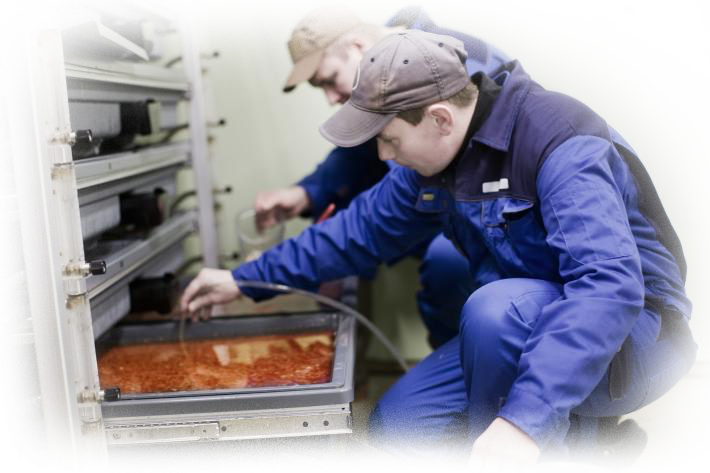
The salmon eggs are transported to a hatchery once they have been fertilized. Here, the eggs lie submerged and closely monitored in freshwater tanks. The eggs require optimal temperature and sufficient levels of oxygen, and the dead eggs must be swiftly sorted out. A well-managed, efficient hatchery is dependent on smart, technological solutions.
The aquaculture industry depends on highly advanced technologies from companies all over Norway. Navigate right to explore these.
Hatchery
Skala Maskon
All the salmon roe in the hatcheries must be sorted. This was previously done by hand and was very time-consuming. Now, robots have been developed to carry out this job much faster. AGM Roesorter was developed in a collaboration between AquaGen and Skala Maskon, a company specializing in automation for different industries. The robot spends just one hour on a job that would previously have taken over 30 man-hours, and in doing so, making the sorting of roe considerably more efficient.
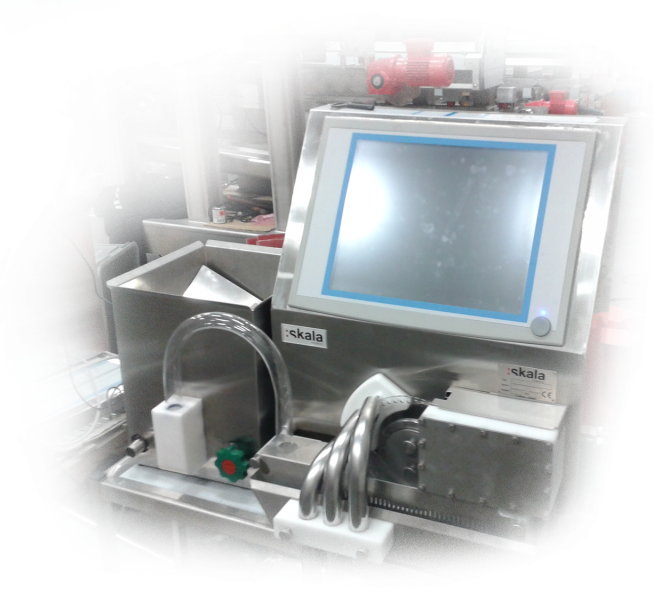
Hatchery – Fry Farming
Fry farming facilities
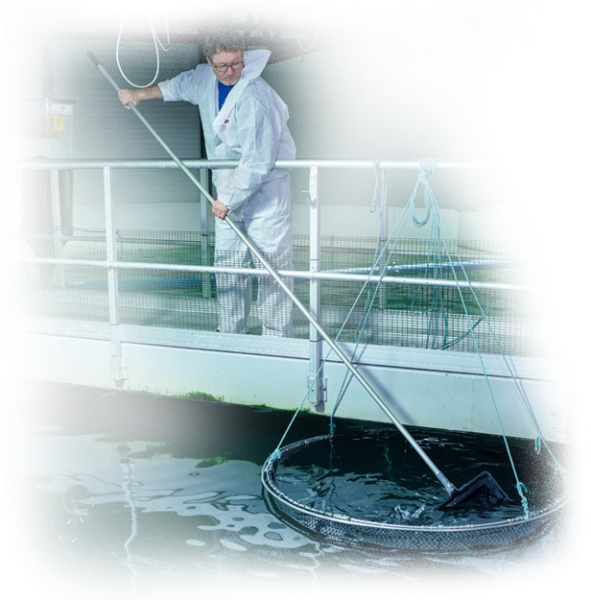
When the small yolk-sac fry are ready to eat other foods, they are transferred from the hatchery to a fry facility. For the next year, they swim and develop in freshwater tanks. The little salmon develop from yolk-sac fry to parr, and later to smolt. After the smoltification, they are ready for life in the aquaculture pens at sea.
Hatchery – Fry Farming
Pharmaq
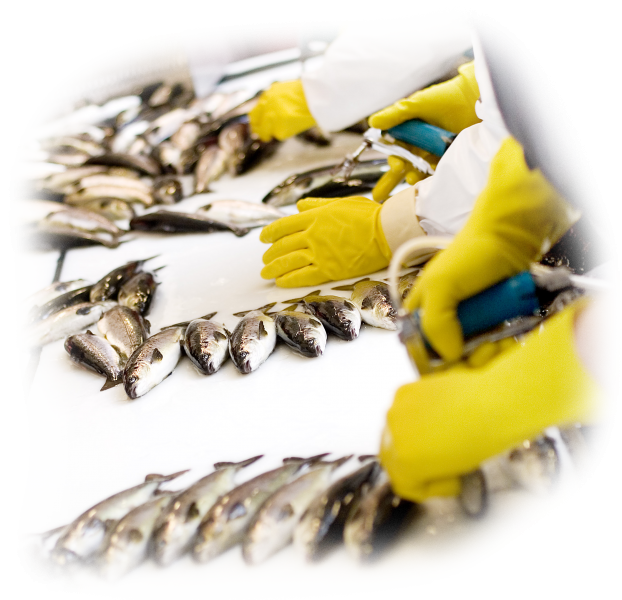
Vaccines for salmon have been crucial to the growth of the aquaculture industry. In the early days of fish farming, they had numerous diseases in the pens, and infected fish were often treated with antibiotics. Since the mid 80´s, the rate of antibiotic use has decreased dramatically, and now it is rarely being used in the treatment of fish. Pharmaq AS is a company that produces vaccines and pharmaceuticals for farmed fish.
Hatchery – Fry Farming
Skala Maskon
Just as for humans, vaccines have improved the lives and welfare of farmed salmon. Salmon vaccines are usually injected by hand. In other words, each salmon gets injected with a syringe containing the vaccine. This is time-consuming work. Skala Maskon has developed an automatic vaccination machine able to vaccinate 20 000 smolt in just one hour. This means that a lot of work, previously performed by workers, can now be left to the vaccination machine.
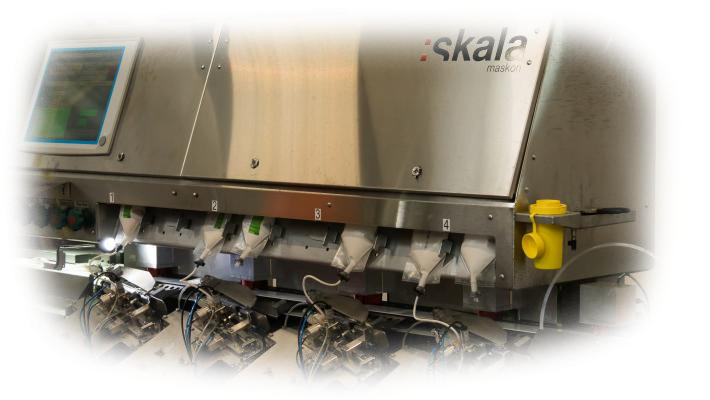
Hatchery – Fry Farming
Recycling plant in Gjøvika
Most of the hatcheries and fry facilities built in Norway today make use of a recycling plant (RAS). The RAS facilities use much less freshwater then older facilities. In theory, more than 99 % of the water can be recycled and reused. Another advantage of RAS-facilities is that they ensure stable environmental conditions for the salmon, without using a lot of energy on heating or cooling the water.
SalMar’s hatchery and fry facility in Gjøvika is an example of a facility that uses the RAS-technology. The facility was ready for use in January 2017 and has the capacity to produce 37 million smolt each year.
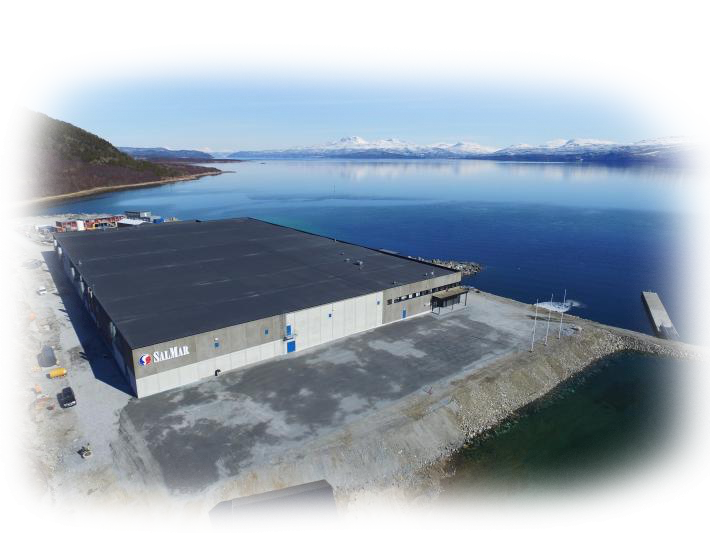
Marine Enclosures
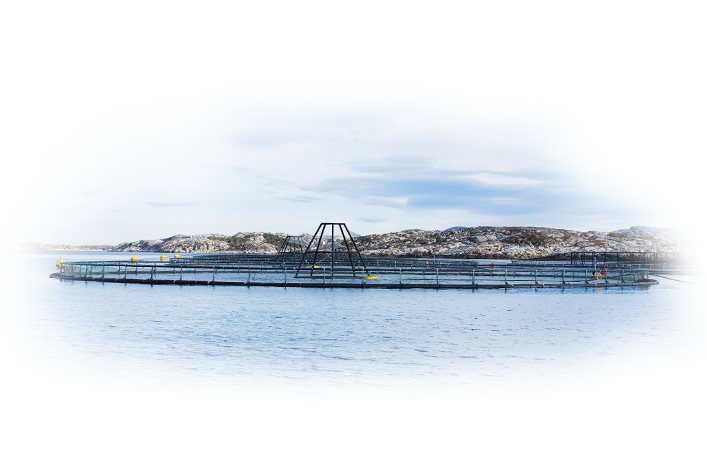
When the salmon have gone through the smoltification process, they are adapted to life in saltwater and get transferred to the sea. The salmon have plenty of space in the pens; when the fish are fully-grown, the pens contain no more than 2,5 % fish. The rest is water. Usually, the salmon spend 12-20 months in the sea, before being transported to the processing plant, before finally reaching the markets in Europe and the rest of the world. The salmon usually weigh between 4 and 6 kilos when they are harvested.
The aquaculture industry depends on highly advanced technologies from companies all over Norway. Navigate right to explore these.
Marine Enclosures
Hydrolicer
Sea lice is one of the biggest challenges for the marine facilities, and the industry spends billions of kroners yearly attempting to resolve it. The Hydrolicer is one of the technological solutions being used to remove sea lice. The salmon are transferred to a closed container where water is moving in a fast eddy current. This creates pressure differences, forcing the lice to detach from the salmon.
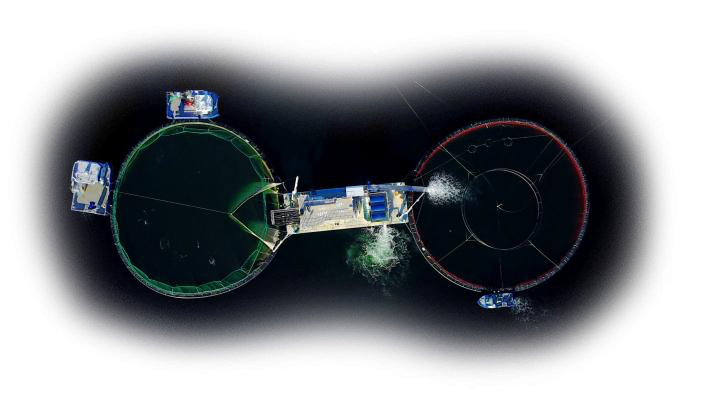
Marine Enclosures
Aqualine
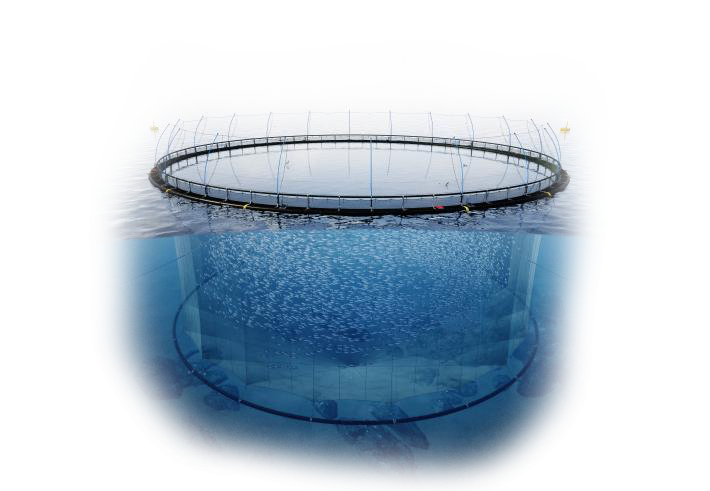
Escape of farmed salmon has been a challenge for the farmers since the 1970’s. Through the development of new aquaculture pens, escape has become a significantly lesser problem. Aqualine Midgard System is an example of such a pen. The bottom ring is attached directly onto the net to ensure that the pen system moves the correct way, keeping damage to the net at a minimum. Pens have also developed to make it safer for the technicians to move on the edge of the pen, even in bad weather.
Marine Enclosures
Sperre
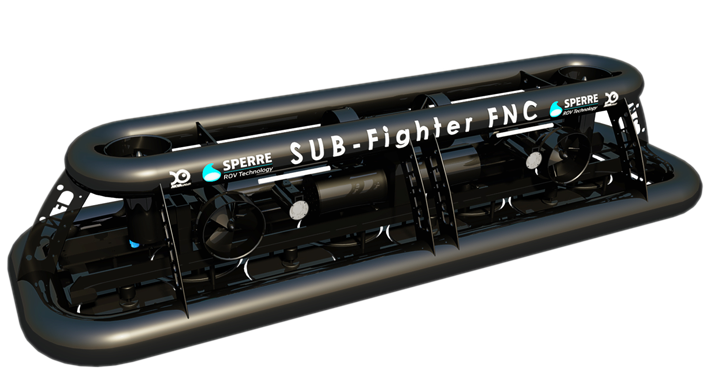
Fouling of the net can decrease the water quality within the pen. Commonly, divers and net washers are employed to remove fouling, but in an increasing number of instances, remote-controlled submersibles (ROVs) are now being used. The Norwegian company, Sperre, delivers ROVs with a high-pressure washer to clean the nets. The submersible can work 24 hours a day and is more cost and work efficient.
Marine Enclosures
Steinvik
Steinsvik is a Norwegian company delivering advanced feeding systems, enabling the aquaculture companies to remotely feed several facilities at once from a centralized feeding center. SalMar has established a remote feeding center on Senja, an island in Troms. The people working here feed the salmon in all of Salmar’s facilities across Troms and Finnmark.

Marine Enclosures
Ørnli Slipp
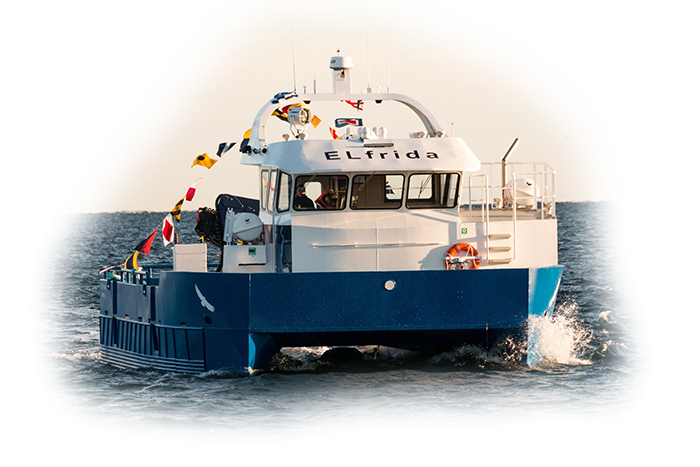
The world’s first electrified service boat, ELfrida, was delivered to SalMar in February 2017. The boat came to life as a collaboration between Ørnli Slipp, SalMar and Siemens. ELfrida is based on brand new technology, and the boat is an electrical hybrid that can be charged at the dock. The environmentally friendly electrical motor reduces the use of fossil fuel energy within the aquaculture industry.
Processing Plant
Processing and distribution
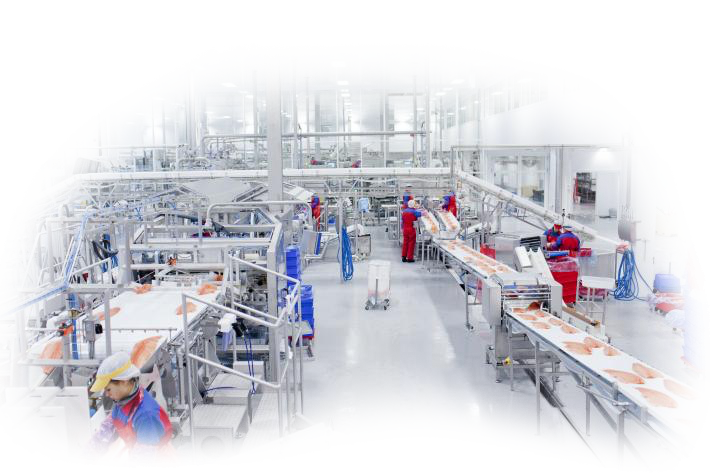
At this point, the salmon are ready for harvesting, and within a short period, they end up as delicious meals on tables across the world. Today’s processing plants are highly advanced technological facilities with robots and humans working side by side in order for the process to be both gentle and efficient.
At the plant, the fish are processed and made ready for shipment to customers in various countries. The majority of the fish are used for human consumption, but the parts that we do not eat are turned into other products.
The aquaculture industry depends on highly advanced technologies from companies all over Norway. Navigate right to explore these.
Processing Plant
InnovaMar
InnovaMar was completed in 2010, on Frøya in Trøndelag – and is one of the world’s most innovative facilities for the docking and processing of salmon. The facility has an area of 17 500 square meters, which corresponds to two and a half football courts! InnovaMar has the capacity to slaughter 150 000 tons of salmon every year. This is equivalent to about half of all the salmon that is produced in the mid-region of Norway. The facilities have many innovative and high-tech solutions, which take into account both the fish that are being processed and the humans working there. Every day, over 600 people work with the slaughtering and processing of fish, as well as the administration.
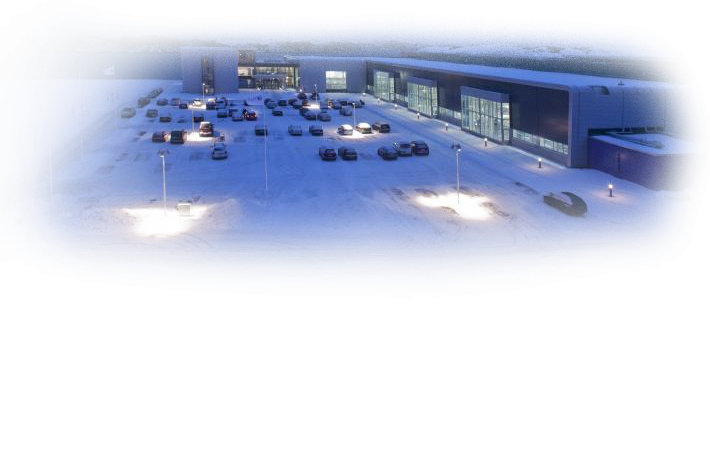
Processing Plant
InnovaNor
InnovaNor is a modern fish processing plant in Senja municipality. The factory was completed at the end of 2021 and has over 300 permanent employees today.
The facility covers an area of 20,000 square meters, and it has an annual capacity to slaughter 150,000 tons of fish. The facility has its own fillet line with a capacity of 15,000 tons per year.
Inside the factory, the administration of SalMar also has its offices, together with the feed center which can remotely feed all production facilities for SalMar in Northern Norway.
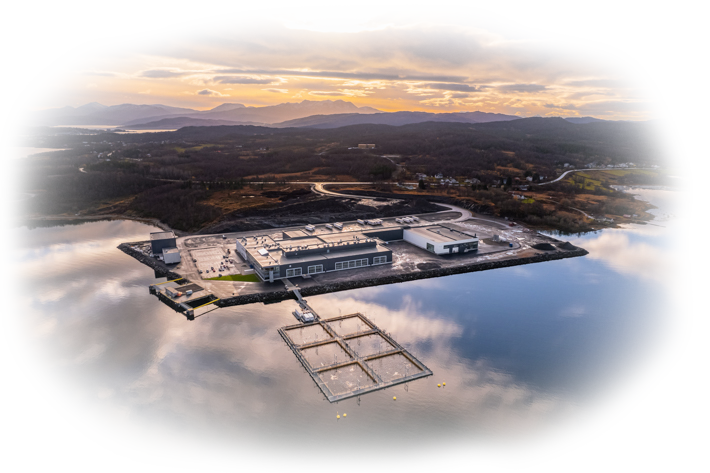
Processing Plant
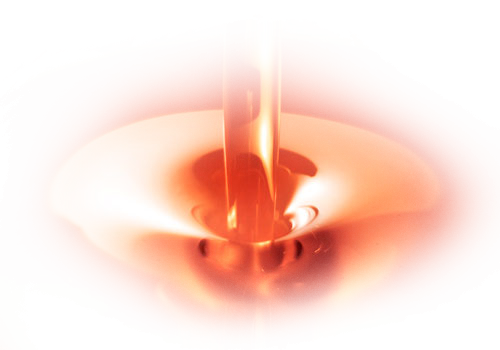
Nutrimar
At InnovaMar the salmon are processed. Blood and intestine are removed, and they are transported by vacuum pipes to the next-door company, Nutrimar. The waste is processed into oil of high quality, protein concentrate and protein meals. These are used as ingredients for animal feed. The close cooperation with SalMar gives the company the unique possibility of creating value through a bi-product of farmed salmon.
Challenges and solutions
Challenges and solutions
Salmon farming is a young industry – and as you see on the screen, it has seen rapid development since its beginning, almost 50 years ago. There have been several challenges connected to the welfare of fish and the environmental impact of the industry which have been resolved, however, there are still other challenges requiring work and attention. These include sea lice, disease, escaping and local environmental impacts.
Good welfare of fish and the environmental status of the industry is important in itself, but these conditions are absolutely crucial for efficient production of salmon. The aquaculture industry uses a large amount of resources on constantly improving the fish health and limiting the impact on the environment.
Navigate to the right to learn more about the aquaculture industry’s challenges and how they work to resolve them.
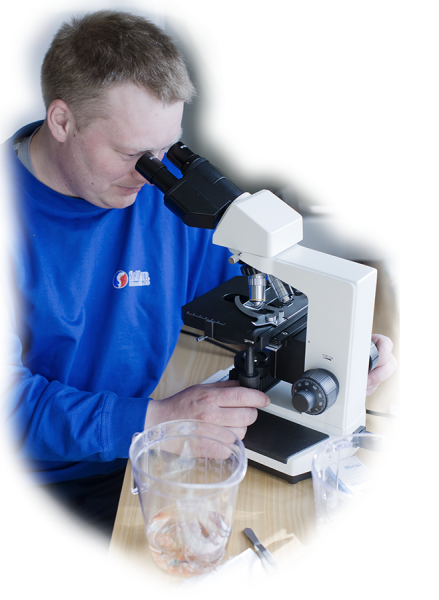
Challenges and solutions
Sea lice
Sea lice is one of the biggest challenges for the aquaculture industry today. It is a small crustacean that we find naturally in the sea. It is important to the health of the wild salmon that the level of lice is kept as low as possible. Therefore, strict rules have been introduced on the permitted level of lice in the facilities.
The sea lice do not affect the quality of the salmon or food safety, but if there are too many, they will harm the welfare of the fish. The farmers conduct weekly counts to monitor the amounts of lice on the salmon. If there are too many, the fish will need treatment. In earlier days, the treatment for sea lice was simply to use pharmaceutical methods, but nowadays, alternative methods have been developed to remove the lice. Among the alternative treatments is the use of cleaner fish that eat the lice from the salmon, and the use of hosing, making the lice fall off the fish. The main strategy, though, is through preventive measures, like the use of protective covering around the pens that stop the lice entering.
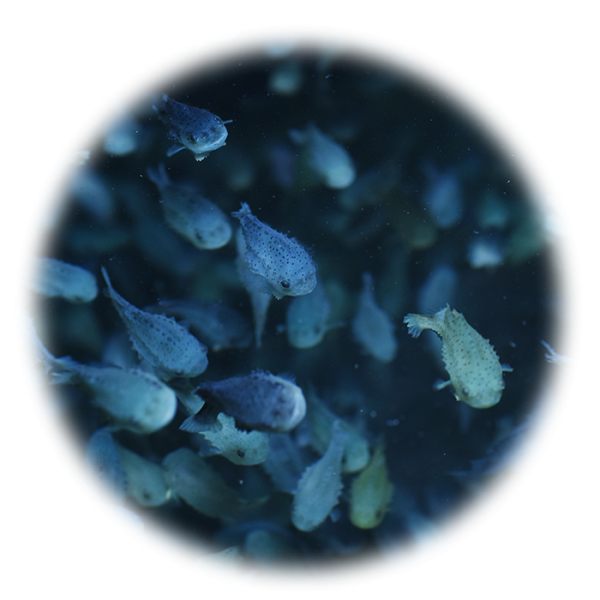
Challenges and solutions
Disease
The health of the fish is of a high priority and the aquaculture industry uses various methods to prevent disease. Vaccination and good hygiene routines, alongside the breeding of robust salmon, are the most important measures. The location of the facilities ensures good living conditions for the salmon, and fish health personnel visit the facilities regularly.
There are still challenges connected to disease, but there is no doubt that the measurers that have been implemented have had a significant effect. Today, we almost never use antibiotics in Norwegian aquaculture farming. In fact, the aquaculture industry has reduced the use of antibiotics by 99% since 1987. The total use of antibiotics in Norway includes 88% for human consumption, 11% for the treatment of agriculture animals, and just 1% for treatment in aquaculture.
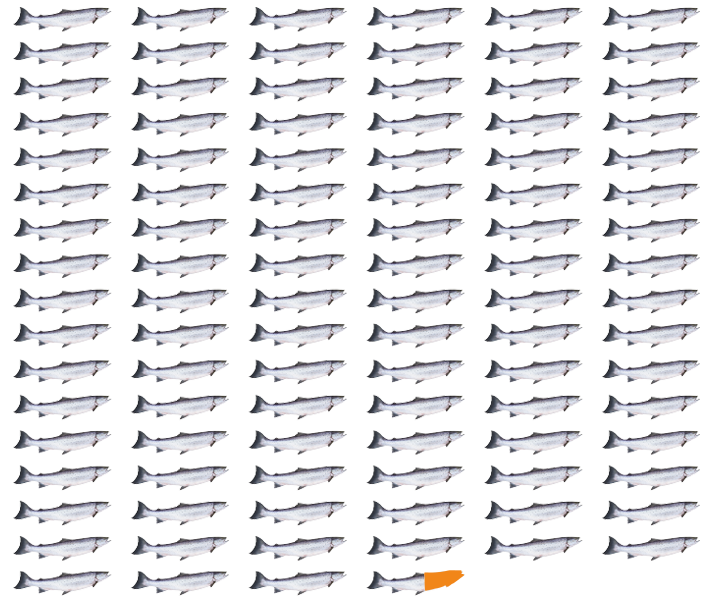
Challenges and solutions
Escape
The aquaculture industry has a zero-escape vision, both because the farmed salmon can mix with the wild salmon, but also because escaped fish equal an economic loss for the farmers.
Holes in the nets can appear after work operations or bad weather conditions. The aquaculture industry actively works on preventative measures through focusing on good routines and the use of correct equipment. These measures have worked, and the number of escapes has gone down steadily in the last decade, despite the doubling of production. From 2006 to 2016, the amount of escaped salmon was reduced by 86 %.
Should an accident still occur, it is the farmers’ duty to report it to the Directorate of Fisheries. In addition, the farmers have to attempt to catch the escaped salmon.
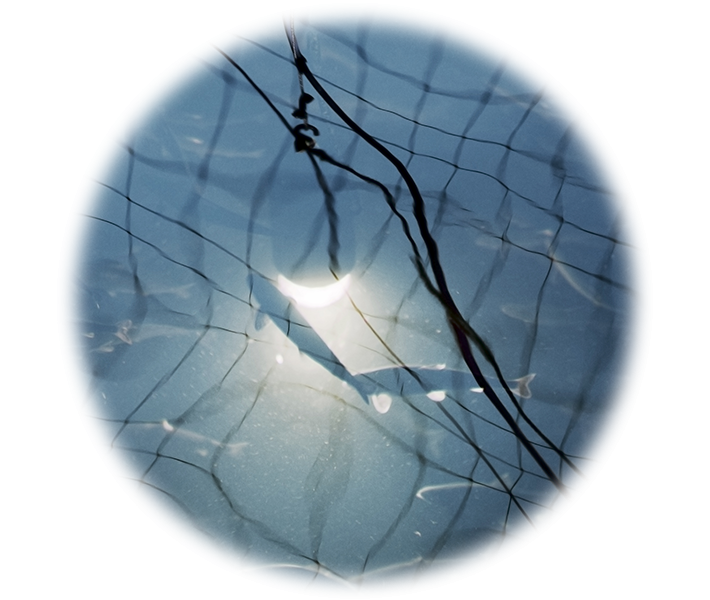
Challenges and solutions
Environmental Conditions Surrounding the Facilities
In aquaculture farming, there are many fish living in small areas. Therefore, the seafloor around the facilities will be impacted to a certain extent, in the form of feed leftovers and feces from the fish.
This may impact other organisms living around the pens, but there is a lot of ongoing work to limit these impacts. The facilities are placed on locations with good water influxes, and with modern technology, the farmers avoid feeding the salmon more than they can eat. The environmental conditions are closely monitored, and all the farmers must regularly collect and send in samples. In addition, all of the facilities must be left empty for at least two months every two years to let the seafloor recover. Over time, the area will return to its original state.
The measures work – almost 90 % of all the aquaculture facilities along the Norwegian coast have an environmental status marked as “good” or “very good”.
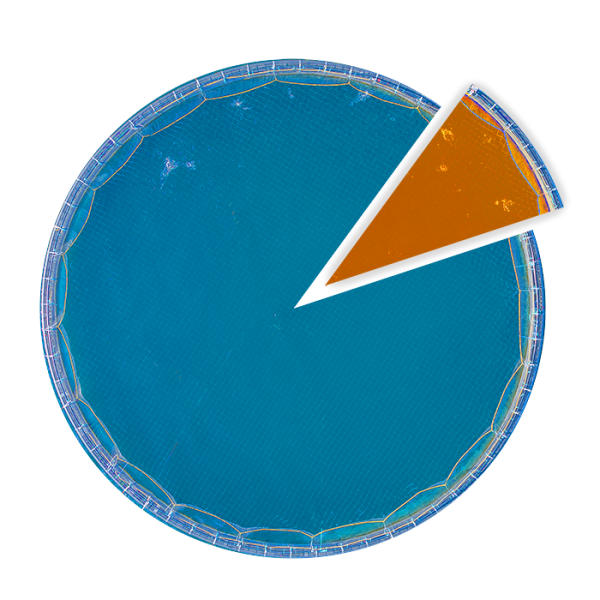